Introduction to Electrospinning
Electrospinning is a cutting-edge technique that enables the production of nanofibers with diameters ranging from nanometers to micrometers. The process involves using high-voltage electric fields to draw charged threads of polymer solutions or melts into fine fibers. Since its inception, electrospinning has gained significant traction due to its ability to create ultra-fine fibers with unique properties suitable for various applications, from medical devices to filtration systems.
How to Optimize the Electrospinning Process and Tune Nanofiber Morphology
To achieve nanofibers with the desired morphologies, three main sets of parameters need to be optimized before and during the electrospinning process: solution properties, operating parameters, and environmental conditions. Solution properties include the molecular weight of the polymer, viscosity, conductivity, and surface tension of the polymer solution. Additionally, the electric current significantly impacts fiber morphology. Operating parameters consist of the applied high voltage, flow rate, and the distance between the spinneret tip and the collector. The solidification of fibers during formation, influenced by the solvent's evaporation rate, depends on environmental conditions. Consequently, changes in environmental factors like relative humidity and temperature also affect nanofiber characteristics.
Solution Parameters:
- Molecular Weight
- Solution Viscosity
- Solution Conductivity
- Surface Tension
Operation Parameters:
- Operation Voltage
- Flow Rate (Feeding Rate)
- Distance From the Nozzle to the Collector
Environmental Conditions:
- Relative Humidity
- Ambient Temperature
- Gas Atmosphere
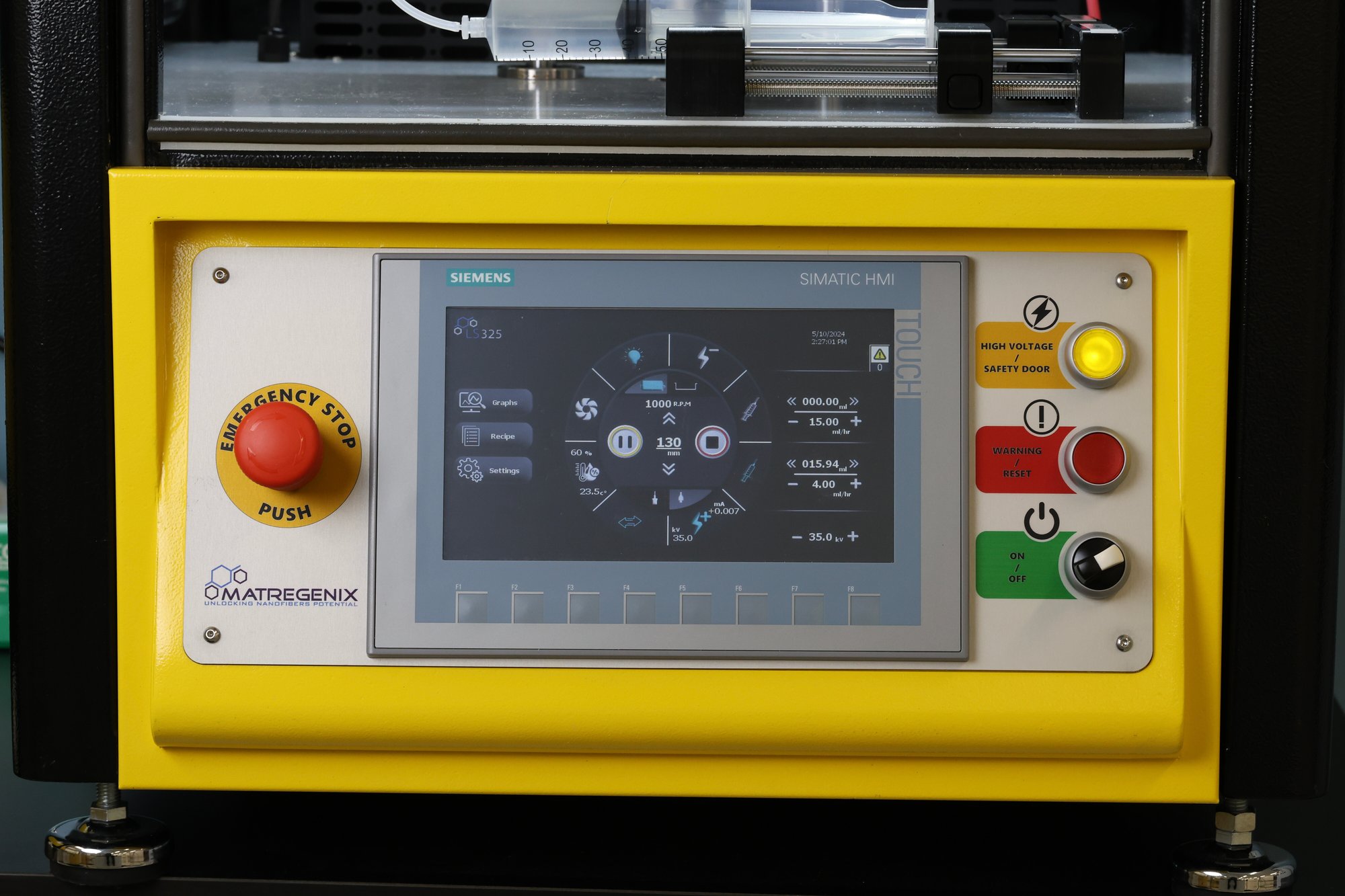
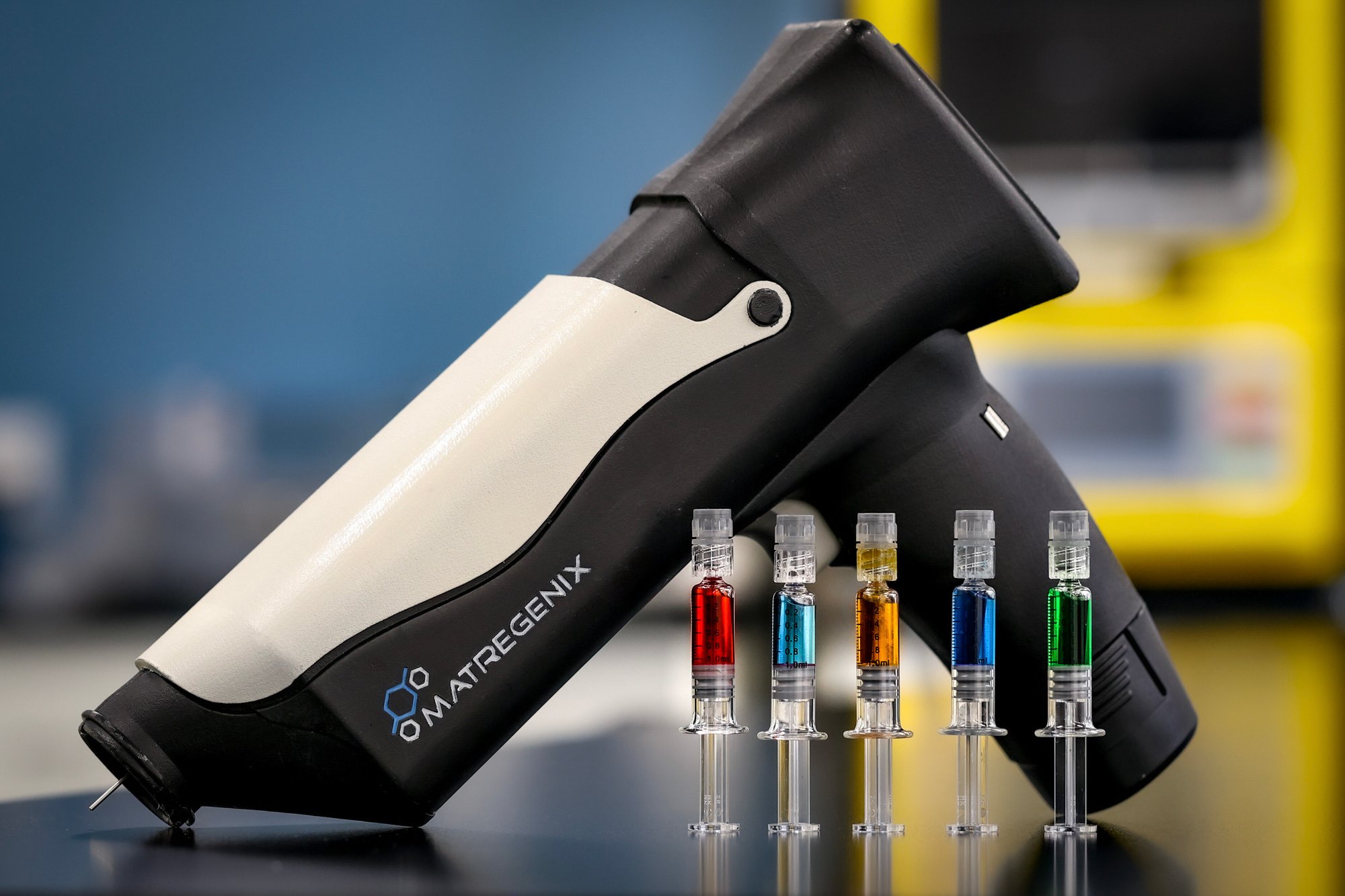
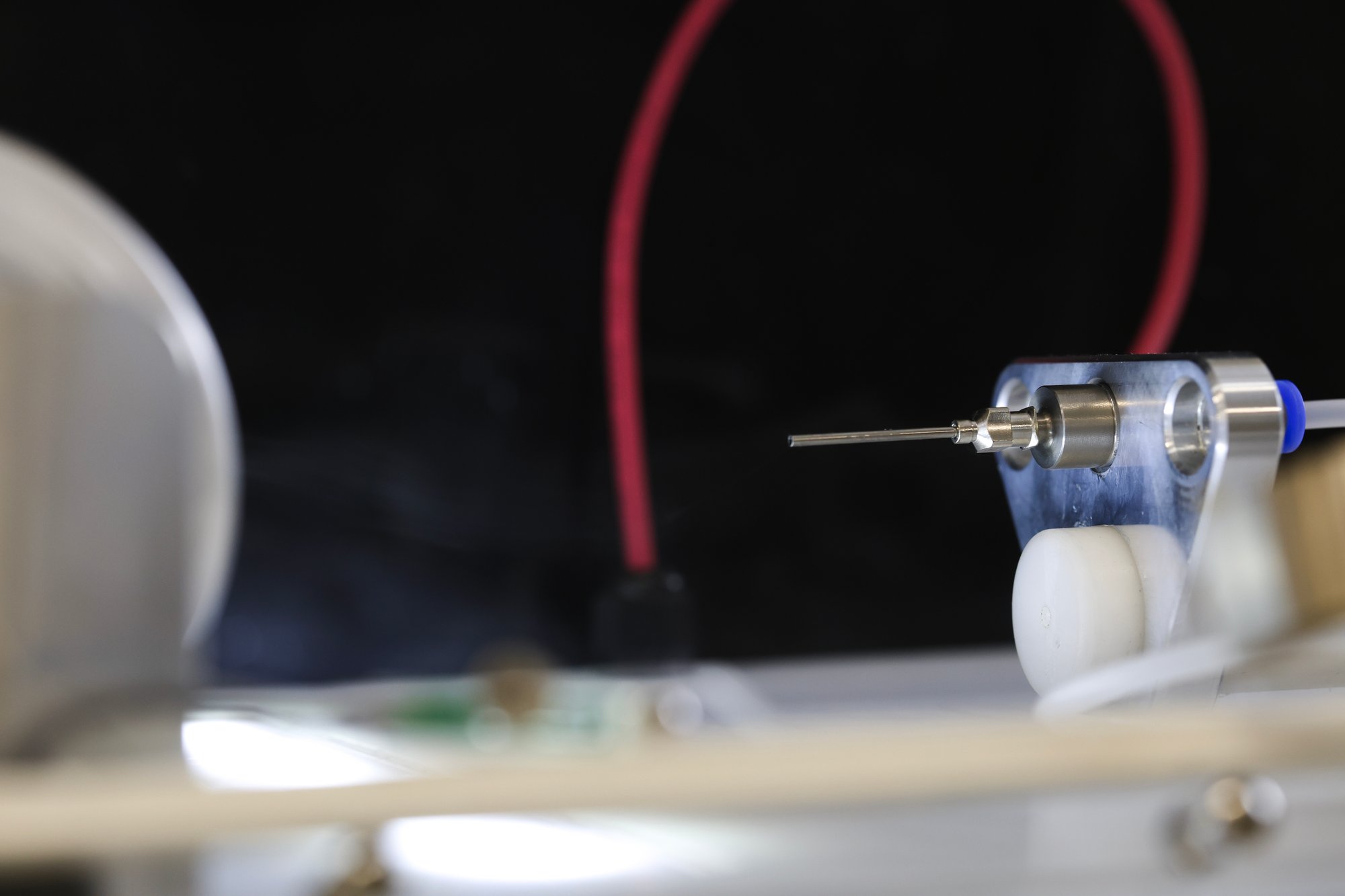
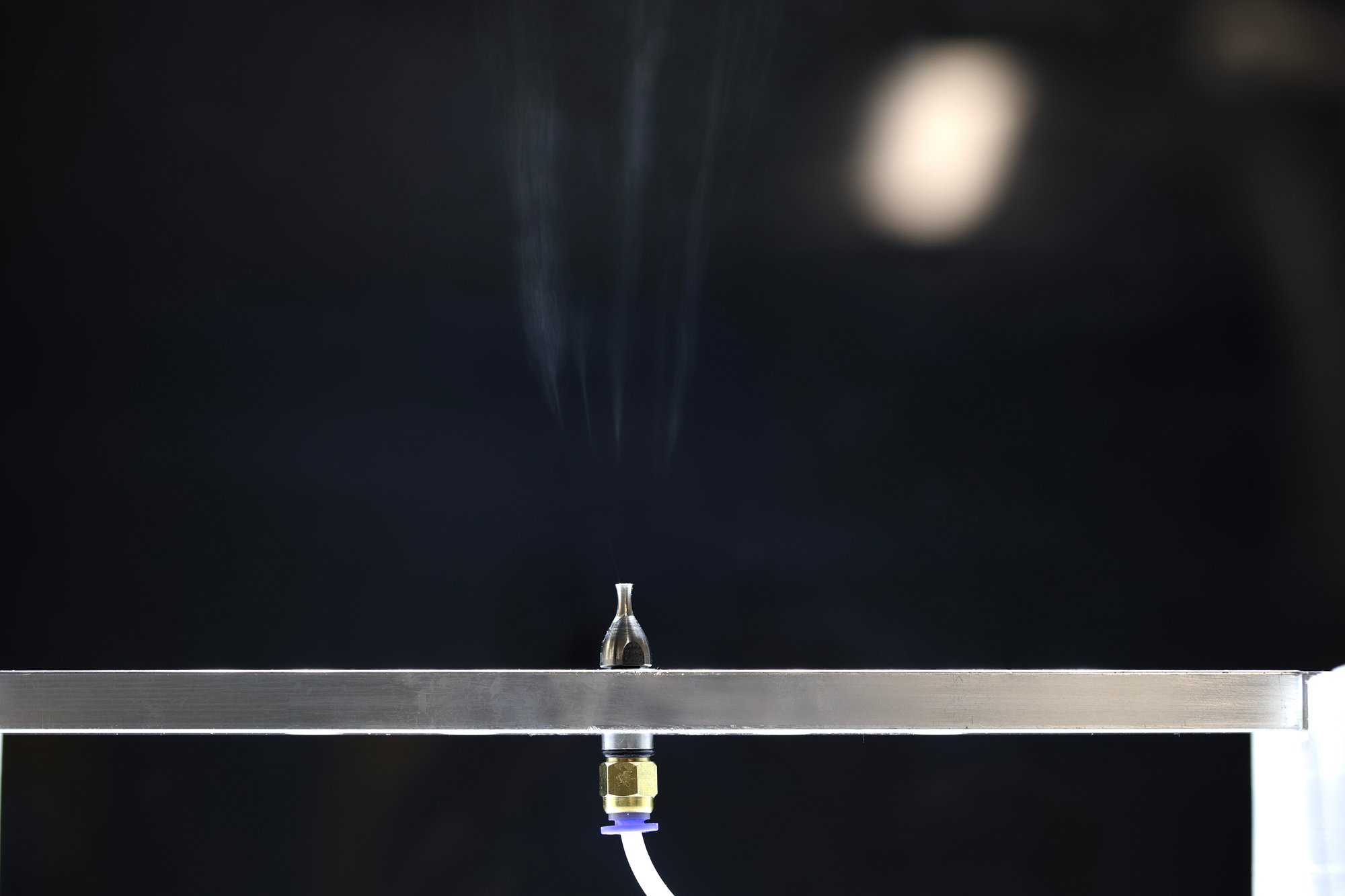
Advantages of Electrospinning for Nanofiber Production and Applications
Electrospinning offers several key advantages for nanofiber production, making it a preferred method in various high-tech applications:
- High Surface Area-to-Volume Ratio: Nanofibers produced via electrospinning have a very high surface area-to-volume ratio, which enhances their interaction with surrounding environments. This property is crucial in applications like filtration, catalysis, and sensor technology, where surface interactions play a significant role.
- Versatility in Material Usage: Electrospinning is compatible with a wide range of materials, including synthetic polymers (e.g., polycaprolactone, polyvinyl alcohol, TPU, PA6, PVDF…), natural polymers (e.g., collagen, chitosan, Silk, Wool, Cellulose, Proteins…), and composites. This versatility allows the creation of nanofibers with tailored properties for specific applications.
- Customization of Fiber Properties: The electrospinning process can be finely tuned by adjusting parameters such as voltage, solution concentration, flow rate, and collector distance. This customization enables precise control over fiber diameter, porosity, and alignment, which is essential for developing application-specific nanofibers.
- Scalability: Electrospinning can be scaled from lab-scale research to industrial-scale production. Advanced setups, such as needleless systems, significantly increase production rates, making it feasible to produce nanofibers in large quantities for commercial use.
- Cost-Effectiveness: Compared to other nanofiber production methods, electrospinning is relatively cost-effective. The equipment required is less expensive, and the process itself is straightforward, involving the use of readily available materials and solvents.
Nanofiber Applications
There are a number of applications that have been identified where nanofibers are poised to offer unique solutions.
- Applications in Filtration: Electrospun nanofibers are highly effective in air and water filtration systems. Their fine porosity allows them to trap particles, bacteria, and viruses efficiently. Studies have shown that nanofiber filters can achieve filtration efficiencies of over 99.9% for particulate matter.
Examples applications of electrospun nanofiber membranes in the filtration industry include: Air filters such as hepa filters, MERV, N95/N99 and others, in addition to liquid filters, such as filters used in wastewater management systems, or oil filtration systems.
- Medical Applications: In the medical field, electrospun nanofibers are used in wound dressings, drug delivery systems, and tissue engineering scaffolds. Their high surface area and porosity facilitate cell attachment and proliferation, making them ideal for regenerative medicine. Additionally, an interesting approach is the use of core-shell or bi-component nanofibers as drug carriers, as they can be loaded with therapeutic agents for controlled drug release. This is usually obtained by using a coaxial nozzle.
An example of a product using this technology is MatriNova, a groundbreaking advancement in biomedical technology developed by nanofiber company Matregenix in Mission Viejo, CA. MatriNova utilizes nanofiber technology to create a non-biological, antimicrobial, programmable fiber matrix similar to a human extracellular matrix.
- Energy Storage: In energy storage devices, such as batteries and supercapacitors, electrospun nanofibers serve as separators and electrodes. Their high surface area enhances the electrochemical reactions, leading to improved energy storage capacity and efficiency. For instance, electrospun nanofibers have been used to create separators with high thermal stability and ionic conductivity, which are crucial for the performance of lithium-ion batteries.
- Textile Applications: Electrospun nanofibers are used to create high-performance fabrics with enhanced properties such as breathability, durability, and protection. These fabrics are employed in sportswear, protective clothing, and smart textiles. The flexibility and lightweight nature of electrospun nanofibers make them suitable for wearable technology and electronic textiles .
One example of these textile performance products is The North Face company, with its new Futurelight material, a nanospun performance fabric.
Types of Electrospinning Machines, Major Players, and Drawbacks
Electrospinning machines are categorized based on their design and production capabilities, each type having its unique set of advantages and drawbacks.
Needle-Based Electrospinning
Needle-based electrospinning is the most traditional method, involving the use of single or multiple needles to produce nanofibers. This method allows precise control over fiber diameter and morphology. There are several configurations within this category:
- Single Needle Electrospinning: Typically used in laboratory settings, single needle electrospinning setups are ideal for research purposes due to their simplicity and precision. However, the production rate is limited, usually yielding only a few milligrams to grams of nanofibers per hour.
- Multi-Needle Electrospinning: To increase production rates, multiple needles can be used simultaneously. For example, the Fluidnatek LE-500 from Bioinicia features a multi-needle array that can produce nanofibers at higher throughput. Challenges still exist, including needle clogging and uneven electric field distribution which can affect fiber uniformity and overall consistency. This process can be extremely difficult to manage, with high volume production sometimes trying to utilize more than 200 needles at a time in a single machine.
- Nozzle-Based Electrospinning: Some needle-based systems use nozzles instead of traditional needles. For instance, the lab-scale electrospinning systems, LS-200 and LS-325 by Matregenix, utilize a nozzle-based approach to enhance production efficiency. This approach reduces clogging issues, and improves production rate compared with needle based electrospinning systems.
Needleless Electrospinning
Needleless electrospinning offers a significant advantage in terms of scalability and production efficiency. These systems do not use needles but instead utilize alternative mechanisms to generate nanofibers.
- Rotating Drum/Disc Electrospinning: This method involves a rotating drum or disc partially submerged in a polymer solution. As it rotates, the solution is drawn into fibers by the electric field. For example, the NanoSpinner24 from Inovenso employs this technique to achieve higher production rates. Needleless systems like these can produce several grams of nanofibers per minute, making them suitable for industrial applications.
- Spider Spinning Technology: A notable example of needleless electrospinning is the Nanospider technology developed by Elmarco. This method involves a wire electrode partially submerged in the polymer solution. When high voltage is applied, the polymer is drawn into fibers from multiple points along the wire, mimicking the way a spider spins its web. The Nanospider machine can produce nanofiber membranes at rates exceeding 1,000 square meters per hour, making it one of the most efficient industrial electrospinning systems available. However, these systems require higher initial investments and complex setups, which can be a barrier for smaller operations.
Major Players in the Electrospinning Industry
The electrospinning industry features several key players, each contributing to advancements in technology and production capabilities:
- Inovenso: Known for its lab-scale and pilot-scale electrospinning equipment, Inovenso provides versatile and high-precision machines like the NanoSpinner24. These machines are widely used in research institutions and small-scale production facilities due to their flexibility and ease of use.
- Elmarco: A leader in industrial-scale electrospinning, Elmarco’s Nanospider technology is renowned for its high throughput and efficiency. The company focuses on large-scale production, making it a preferred choice for industries requiring bulk nanofiber production.
- IME Technologies: Specializing in custom-built electrospinning machines, IME Technologies offers both needle-based and needleless systems. Their machines are designed to meet specific industrial needs, providing solutions for diverse applications from medical devices to filtration systems.
- Matregenix: An industry leader in electrospinning solutions for biological, filtration, and textile applications. Matregenix offers customized product solutions as well as machinery for a wide range of novel nanofiber applications.
- Bioinicia: Bioinicia’s Fluidnatek line includes advanced electrospinning and electrospraying equipment for both research and commercial purposes. Their multi-needle systems are particularly noted for their ability to scale up production while maintaining fiber quality.
- YFlow: YFlow offers a range of electrospinning equipment, including the NS24 nozzle-based system, which enhances production efficiency and reduces common issues like needle clogging. Their machines are used in both research and industrial settings.
Future Prospects of Electrospinning Technology
The future of electrospinning technology is bright, with several promising developments on the horizon:
- Scalability: Efforts are underway to improve the scalability of electrospinning processes, enabling higher production rates without compromising fiber quality.
- Material Diversity: Research is focused on expanding the range of materials that can be electrospun, including composites and biopolymers, to cater to more applications.
- Process Optimization: Innovations aim to make the electrospinning process more efficient and less energy-intensive, reducing operational costs.
- Smart Fibers: Integrating functionalities such as sensors and actuators into electrospun fibers is a key area of development, opening up advanced applications in smart textiles and wearable technology.
Matregenix Electrospinning Machine
At Matregenix, we leverage cutting-edge electrospinning technology to produce high-quality nanofibers tailored to various applications. Our proprietary processes utilize a modular design that can operate both needle-based (nozzle) and needleless (slot) electrospinning systems, offering flexibility and efficiency in production. This modular approach allows us to switch between different setups based on the specific needs of a project, ensuring optimal performance and cost-effectiveness.
Our decision to utilize a modular design stems from the need to overcome the shortcomings of both needle-based and needleless electrospinning systems. By integrating both methods into a single, versatile platform, we can achieve the precision and control of needle-based electrospinning while also harnessing the high production rates of needleless systems. This flexibility enables us to tailor our processes to the unique requirements of each application, ensuring the highest quality and efficiency. We precisely control parameters to ensure the production of fibers that meet our clients’ specific requirements. Additionally, we are committed to sustainability and efficiency, implementing processes that minimize waste and energy consumption.
By understanding the intricacies of electrospinning machines and staying abreast of technological advancements, Matregenix remains at the forefront of nanofiber production, driving innovation across multiple industries. Whether for medical, filtration, or textile applications, our electrospinning solutions are designed to meet the highest standards of performance and reliability.